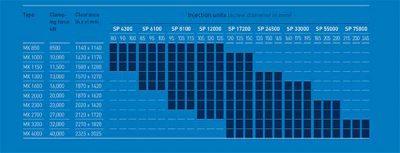
First-class plasticization, precise injection unit
Exact in performance tuning, wear-resistant in operation
Outstanding shot weight consistency combined with first-class repeatability
Take advantage of unlimited precision. The proven in-line injection unit with its rotary piston design transmits the force centrally via the injection piston onto the screw. Injection regulation of pressure and speed is a standard feature of the MX Series. It guarantees you maximum process stabilityand first-class repeatability.
Maximum productivity
The MX Series offers you a choice between hydraulic and electric screw drives. The electric drives enable plasticization in parallel to other machine movements, thereby creating a further increase in productivity.
High throughput with outstanding melt quality
Our plasticizing systems are characterized by their excellent melt quality andcover a broad range of applications for an extremely wide variety of plastics. Thanks to our years of experience and technological expertise, we understand the complex operations involved in plasticization. This is why we can guarantee a high melt specification, high throughputs and optimum melt quality. Choosing the right plasticizing system can improve the quality of your products and increase value retention.
The right screw for every plastic
In order to provide an ideal solution for the processing requirements of different polymers, we have developed material- and processing-specific plasticizing systems. In addition to outstanding melt quality and high throughputs, high-tech plastics mostly require additional wear protection against adhesion, abrasion and corrosion. As a result, service life is also extended. Depending on the part requirement, special plasticizing systems containing specific screws, non-return valves and cylinder fittings are available to you. Using our plasticization systems, you can process the following materials, among others:
– PC and PMMA materials
– Short and long glass-fiber reinforced plastics
– Blends
– Recyclates
Plasticization is our core competence. In this area, there are virtually no limits set on your material-specific requirements.
Impressive tour around the
MX injection molding machine
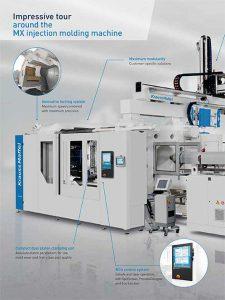
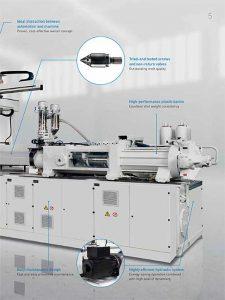
Maximum modularity
-Customer-specific solutions
Innovative locking system
-Maximum speed combined with maximum precision
Compact dual platen clamping unit
-Absolute platen parallelism for low mold wear and first class part quality
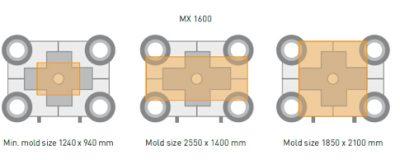
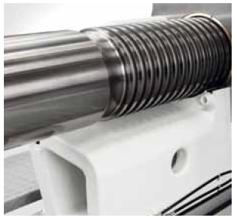
Compact dual platen clamping unit
Robust in design, fast in production and low-maintenance in operation
The MX Series from KraussMaffei is your solution for demanding tasks. Its hydro-mechanical dual platen clamping unit is characterized by maximum reliability and flexibility. Force flow-optimized sliding shoes in combination with guided tie bars guarantee exactly parallel clamping movements and permanent mold protection. The intelligent locking concept ensures extremely short locking times.
Absolute platen parallelism thanks to innovative clamping technology
Force flow-optimized sliding shoes reliably support the moving mold fixing platen as it travels on the machine bed. The sliding shoes are guided horizontally at the side. Even for very heavy molds and maximum opening widths, exact platen parallelism is guaranteed at all times. In addition, the tie bars are permanently guided via guide bushings. The dynamic movement is produced by two movement cylinders which are arranged diagonally and positioned on the outside.
Very short locking times – bringing innovation, even down to the smallest detail
The hydro-mechanical fourfold locking on the tie bars is carried out by saw-tooth shaped elements behind the moving platen which mesh together. It is designed for very short locking times combined with precise positioning. The even application of force through progressive tooth flank play and the friction optimized material combination of brass and steel together ensure maximum service life.
Building up clamping force quickly and reliably
The special pressure pads of the MX Series allow clamping force to be built up very quickly, and the pads always position exactly. The clamping force is built up at precisely the same time on all four tie bars.
Low-maintenance operation
Self-lubricating guide bushes and slide rails with centralized lubrication ensure low-maintenance and trouble-free operation.
Discover our fiber composite solutions for advanced lightweight components:
KM_BR_Faserverbund_en
KM_BR_Werkzeuge_en